Ultrasonic welding has become an essential technology in industries such as automotive, electronics, medical devices, and packaging due to its precision, efficiency, and the high-quality bonds it creates.
One of the most effective frequencies for ultrasonic welding is 35kHz, which strikes a perfect balance between energy efficiency, precision, and high weld quality.
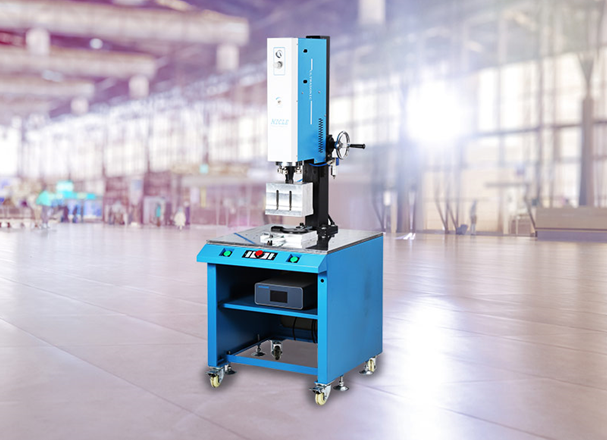
In this article, we will explore how the 35kHz ultrasonic plastic welder improves weld quality, reduces cycle times, and minimizes material distortion compared to other welding methods.
Understanding 35kHz Ultrasonic Welding
Ultrasonic welding uses high-frequency sound waves to generate heat at the welding interface, joining two materials together. The ultrasonic vibrations cause rapid frictional heat at the point of contact, melting the plastic and forming a strong bond. While ultrasonic welding can operate across a wide range of frequencies (from 20kHz to 70kHz), 35kHz ultrasonic welding machines are particularly popular for achieving optimal results.
35kHz ultrasonic plastic welding is suitable for a wide range of materials, especially plastics, and is often used in industries that require precision and minimal material distortion. The frequency is particularly effective for delicate and thin plastic materials, ensuring high-quality welds without excessive heat.
1. Improved Weld Quality with 35kHz Ultrasonic Welders
One of the primary reasons for choosing a 35kHz ultrasonic welding machine is the superior weld quality it offers. Ultrasonic welding at this frequency provides better control over energy delivery, leading to stronger and cleaner welds.
Precision and Energy Control
The 35kHz ultrasonic plastic welding machine provides excellent energy control, allowing for more precise and consistent energy transfer to the welding area. This level of precision ensures that the welds are of high strength without over-welding, which can lead to material degradation or weak spots in the joint. The focused energy at the weld interface results in:
Uniform weld strength: The uniform distribution of energy creates consistent and reliable welds, which is particularly important for sensitive applications like medical device manufacturing or electronics.
Minimal spatter and contamination: The controlled nature of 35kHz ultrasonic welding produces clean welds, reducing the need for post-weld cleaning and ensuring minimal contamination during the process.
High-quality bond: The strength of the bond created by the 35kHz ultrasonic welding machine ensures that the welded joint can withstand high stress without compromising the integrity of the material.
For industries where high-quality ultrasonic plastic welding is required, such as in the production of electronic components, medical devices, and precision automotive parts, 35kHz ultrasonic plastic welders provide optimal results.
2. Reduced Cycle Times with 35kHz Ultrasonic Welders
Another significant advantage of 35kHz ultrasonic welding machines is the reduced cycle time, which is essential for high-volume production. Unlike traditional welding processes, ultrasonic welding operates quickly, and 35kHz ultrasonic plastic welders can produce welds in fractions of a second.
Speed and Efficiency
The energy transfer at 35kHz is highly effective and rapid, which means the welding process occurs almost instantly. For example, typical ultrasonic weld cycles can range from 0.1 to 1 second, compared to the several minutes it takes for other processes like MIG or TIG welding.
The 35kHz ultrasonic plastic welding process generates heat precisely at the point of contact, reducing the need for extended heat application. This results in:
Faster production cycles: With reduced cycle times, manufacturers can increase throughput and production rates without compromising on quality.
Optimized energy use: The rapid heating and cooling process of a 35kHz ultrasonic welding machine makes energy consumption more efficient, reducing costs over time and allowing for more consistent performance.
For high-volume industries, such as the automotive sector or large-scale packaging, 35kHz ultrasonic plastic welding machines enable faster production, leading to better return on investment (ROI). For businesses interested in a more robust and efficient setup, manual ultrasonic welding machines can also play a significant role in improving productivity without sacrificing quality.
3. Minimized Material Distortion
One of the most important benefits of 35kHz ultrasonic plastic welding is its ability to minimize material distortion. Traditional welding methods, such as MIG or TIG welding, can cause unwanted thermal expansion in the material, resulting in warping or distortion. However, 35kHz ultrasonic welders create localized heat at the weld interface, reducing the amount of heat that spreads through the material.
Localized Heat Application
In 35kHz ultrasonic plastic welding, the energy is focused precisely on the welding area, preventing the surrounding material from overheating and distorting. This is particularly beneficial when working with delicate or thin materials, which are prone to warping or shrinking under excessive heat.
Less thermal expansion: The localized heat prevents the entire part from expanding, resulting in minimal distortion.
Ideal for sensitive applications: Industries such as medical device manufacturing, where part precision is critical, benefit from the minimized material distortion that 35kHz ultrasonic plastic welding offers.
Improved product quality: By reducing the amount of warping, the final product has a higher-quality finish and retains its intended shape and size.
In high-precision industries where part quality is crucial, 35kHz ultrasonic welding machines deliver better results by minimizing unwanted distortion in the materials being welded.
4. Applications of 35kHz Ultrasonic Plastic Welders
The 35kHz ultrasonic plastic welding machine is versatile and can be used in various industries. Some common applications include:
Automotive Industry
In the automotive industry, 35kHz ultrasonic plastic welding is used to join components such as dashboards, light housings, and electrical connectors. The speed and precision of ultrasonic welding make it ideal for manufacturing lightweight plastic parts that need to withstand high stress.
Electronics Manufacturing
For the electronics industry, the ability to create small, clean, and reliable welds is crucial. 35kHz ultrasonic welding machines are often used to assemble components like circuit boards, battery packs, and connectors, where precision and the prevention of material damage are essential.
Medical Device Manufacturing
In medical device manufacturing, parts often need to be welded with high precision to ensure proper functionality and sterility. 35kHz ultrasonic plastic welders are commonly used to weld medical-grade plastics for devices such as syringes, IV connectors, and surgical instruments, where weld quality and minimal material distortion are critical.
Packaging Industry
In the packaging industry, ultrasonic welding is used to seal plastic films and containers, ensuring airtight seals. 35kHz ultrasonic welding machines are ideal for producing these quick, efficient, and high-quality seals that maintain the integrity of the product inside.
5. Advantages of 35kHz Ultrasonic Welding over Other Methods
When compared to other welding methods, 35kHz ultrasonic welding offers several clear advantages:
Speed: The rapid welding process of 35kHz ultrasonic plastic welding reduces cycle time compared to traditional welding methods, improving productivity.
High-Quality Welds: The precision offered by 35kHz ultrasonic welders ensures strong, clean, and durable welds, which are particularly important in high-demand industries like electronics and medical devices.
Reduced Material Distortion: Unlike methods like MIG or TIG welding, ultrasonic welding creates localized heat, which reduces the chances of material distortion or warping, ensuring the final product retains its intended shape.
Less Need for Post-Weld Processing: 35kHz ultrasonic welding results in cleaner welds, reducing the need for extensive post-weld cleaning or finishing, which saves both time and money.
Conclusion
The use of 35kHz ultrasonic welders offers a host of benefits, from improved weld quality and reduced cycle times to minimized material distortion. For applications requiring precise control and versatility, a pneumatic ultrasonic welder offers an excellent solution, complementing the capabilities of 35kHz ultrasonic plastic welding machines.
Whether you’re in automotive manufacturing, electronics assembly, medical device production, or packaging, investing in a 35kHz ultrasonic welding machine can significantly enhance your manufacturing capabilities, improve the quality of your products, and optimize your production process.